半導體業是一個發展40多年已經相當成熟、競爭激烈的紅海,尤其臺灣更是晶圓代工的重鎮,大廠各據山頭,一個成立不到2年的半導體新秀,資本額只有12億元,連龍頭廠的二百分之一都不到,如何殺出重圍,站穩腳跟,速度是決勝關鍵,因為公司每分每秒都在燒錢,如何在最短時間將製造系統上線,讓產線能夠順利啟用試產,這是瑞峰半導體IT的責任。
縮短製造系統導入時間,是加快產線啟用試產的關鍵
2016年4月成立的瑞峰半導體,是一家晶圓級封裝服務的半導體高科技新創,專門提供晶圓封裝腳位線路的重布線(RDL),將上游晶圓代工廠提供的一片片晶圓,經過塗布、曝光、顯影等製程加工程序,讓這些晶片可以根據客戶的要求重新客製,能被廣泛運用在手機、TV、車用、家電等終端產品上。
瑞峰成立才隔沒多久,就獲得臺廠重砸上億元投資入股,有了充裕的資金作後盾,如何讓產線能夠盡快啟用試產,成為公司的當務之急。然而,原本隔年1月就要試產,但直到2016年底,這家公司的MES系統都仍未上線,甚至連ERP都沒有,直到瑞峰半導體資訊管理部處長陳如經上任後,才一身扛起了這個重責大任,從無到有加速完成IT建置,以確保能如期讓產線順利啟用。
陳如經是一位在半導體業IT任職將近30年的沙場老將,先後待過世界先進、台積電等知名半導體廠,負責管過資料庫、更跨足MIS到MES等製造相關系統的開發和維運,從前段的IC設計、晶圓生產製造,到後段的封裝測試他幾乎都待過,IT實戰經驗可說是相當豐富。
一般來說,半導體廠建廠時程至少要花費6到9個月。但是陳如經接下資訊主管一職時,瑞峰已經成立8個月了,但公司仍只有籌備處,廠房也在興建中,相關的硬體設備那時才陸續進駐,隔年1月,產線就要啟用試產,因此,只剩不到30天,製造系統就得要推出上線,對陳如經來說,時間相當緊迫。工廠產線啟用已經迫在眉梢,但他更得面臨公司大大小小系統都要資訊部門來建置,對他來說,更是一大沉重的負擔。
在IT系統規畫上,遵循「先求有再求好」策略
他回憶剛進這家公司時,「不僅資訊系統都還沒有,連公司E-Mail信箱都還只有先申請到網域名稱」他說,因為是新公司,一切系統都要從無到有自行建置,但是當時IT部門只有3個人,資訊人力嚴重不足,使得他必須要找出新方法,在最短的時間,來逐一解決這些難題,並且能夠讓產線盡快啟用投入生產,這也成為他上任後首要面對的IT大考驗。
首先,在IT系統規畫上,陳如經遵循「先求有再求好」的策略,先讓系統能夠上線,先滿足使用者基本的運作需求,再逐步完善各項功能。他表示,這樣做的好處,一來有更長時間分散工作量,降低對IT人力的需求,二來初期系統程式不需要經過大幅修改,客製少風險就低,將有助於提高系統的穩定性。
其次,在IT系統建置上,他則依系統上線的輕重緩急,來逐步完成系統的建置。第一步就是先讓核心MES製造執行系統先上線。因為有了MES系統之後,工廠產線才可以順利啟用試產, 甚至陳如經形容:「MES系統等同於製造業的命脈,甚至比ERP系統都還重要。」
正因為MES系統攸關製造業的命脈,導入過程必須步步為營,更要小心謹慎才行,尤其半導體高科技業更是如此,對於製造相關系統有著更高標準的要求。一般而言,從MES導入到正式上線至少需3個月,甚至更久的時間,但是瑞峰卻只剩下30天不到的時間,系統就要上線了。
為了能夠盡可能配合系統上線時程,陳如經採取諸多作法,不僅縮短硬體建置時間,短期內就將整套系統快速部建起來,從硬體進駐,到準備就緒,安裝整套軟體到完成基本系統測試,讓它有基本的運作能力,只花不到兩周就完成;另外也大幅降低前期採購對於客製化的需求,更直接略過廠商Demo測試的步驟,就連要求廠商PoC都沒有,就大膽決定採用,甚至在最後導入過程中,也捨棄一部分項目測試,才讓系統如期上線,讓公司能趕快用它來試產。
瑞峰半導體資訊管理部處長陳如經表示,半導體IT最大任務在於改善產線良率,降低生產成本,替公司創造最大的產能。(攝影/洪政偉)
MES系統不僅兩套互為備援,更要通過HA高可用測試
但陳如經強調,之所以能省略這些步驟,在於原營運團隊成員多半是這方面領域的專家,個個都很有經驗,十分熟諳MES系統,懂得系統所須的製造執行配置與需求,因此,在導入過程中,能夠替他們減少許多不必要測試和除錯的過程,幫助縮短系統上線的時間。
但是即便如此,有些測試還是不能省。陳如經就堅持要求,MES系統上線以前,一定得通過故障轉移(Failover)測試,確保互為備源的兩套MES系統,能夠同時運作,且相互支援,以便在一臺MES系統故障時,還有另一臺可以接手正常運作,以維持系統的高可用性和可靠度。
更大的挑戰是,MES這套系統對系統停機時間的容忍度極低,必須維持機器7X24小時都要能夠正常運作。因為,「製造過程不能中斷」他說,只要系統一出錯,整個產線就會停擺,造成損失慘重。
他估算過,機臺發生當機的代價,假使以一間廠房機臺設備成本為10億元來計算,預估使用年限為五年,只要一臺機臺停機,導致整座工廠產線受牽連,生產延遲的後果,就是每天損失將近60萬元。這還僅僅只是機臺,未包括其他人事成本,以及生產拖延無法如期交貨產生的營業損失。
瑞峰的產線在2017年1月啟用後隨即投入試產,並在5月開始進行小量生產。在將產品提供給客戶驗證後,陳如經更持續擴大MES功能,來提高生產製程的品質,之後更先後整合EAP/RMS/SPC等製造相關系統,讓整個生產過程可以全程自動化,以提高產能,同時也減少人工作業的錯誤。並也逐一改善產線技術人員作業上遇到的問題,例如重新優化UI介面,讓操作更加流暢等。
另在管理方面,陳如經也同步導入ERP系統,秉持先求有再求好的原則,一開始盡量縮減使用者的需求,讓系統先上線再說,例如,初期僅提供會計總帳功能,讓會計人員能用它來完成基本的帳目記錄,其他人事等系統之後才陸續完成。這套ERP系統也在同年10月完成上線。
在IT架構上,陳如經很早就決定導入伺服器虛擬化,來提高硬體使用率與降低管理成本,他表示,目前除了兩臺互為備援的MES系統的資料庫,皆採用實體機器外,其餘系統都改以VM來提供服務,就連ERP系統也都改用VM方式提供原有的管理服務。
ERP上線迄今,資訊部門替它增修不少新功能,像是現在客戶的來料晶片到貨時,ERP系統能自動通知負責的業務與生管人員,讓他們能在第一時間掌握來料的品名與數量等資訊,來與客戶確認,或是將其列入生產排程。同時也將它與MES系統進一步整合,用來簡化使用者在工單下線、完工入庫的處理程序。
在產線方面,瑞峰也透過MES系統整合機臺資訊與客戶的工單系統,打造一套晶圓刻號自動比對系統,能自動比對晶圓刻號與客戶工單紙本上的刻號是否一致,避免拿錯或出錯貨,一旦發現異常會自動通知相關人員,全程皆無須人力介入。陳如經表示,過去以人工比對時,通常一個批號生產25片晶圓,每完成一批貨,人工檢驗就需要15分鐘,若以月產能1萬片來計算,大約一個月會耗費100個小時的人力花在檢驗核對上,現在透過這套系統,將可大幅降低人力需求,也避免人工錯誤,加快整個生產速度。目前這套系統已在今年6月上線。
主打 「少量多樣」的客群,也帶來另一個IT挑戰
雖然瑞峰半導體同屬於接單生產的晶圓代工廠,但不像大廠晶圓代工策略,它反而切入利基市場,轉向小量多樣化接單,這也成為它營運後所遭遇到的另一個IT挑戰。
像是接單量一多時,每個客戶的要求可能都不盡相同。比如十家客戶,每家要求報表格式會不同,出貨標籤也會不一樣。這時IT就必須依每位客戶量身製作一套屬於它完全客製化的需求。對於資訊人員而言,將是一個沉重的包袱。
再者,不像產品訂單量大的大廠接單,機臺生產時只須沿用同一套製程配方,無須更換製程,對於瑞峰來說,因為訴求「少量多樣」的策略,很多都是中小型客戶,生產的產品種類繁多。
為了因應不同產品線,就可能需要常常更換製程,每個機臺所要儲存的製程配方都不一樣,這也使得MES系統需要存取的產品組合變更多,一旦產品種類越多樣時,對於產線人員來說,在檢驗核對時就會容易發生錯誤,「這是在半導體大廠較少遇到的情況」他說。
對此,陳如經的作法是,針對每個重要生產環節加入不同的系統檢驗機制,來幫助使用者進行核對,以減少錯誤的發生。例如工廠每天生產前,系統會自動比對ERP與MES上的客戶料號是否相同, 確保兩者料號都一致等。
不僅如此,陳如經也計畫結合人工智慧,來輔助人工檢驗作判斷,例如,現在以自動光學檢測(AOI)機臺進行檢測掃描時,雖然能找出有瑕疵的晶圓,但要做到瑕疵的分類,仍得仰賴工程師的專業判斷。他期盼未來可改由AI來提供協助,幫助他們解決這個難題。甚至也能用它來提高產線製程品質的穩定度,降低產品良率的差異。「半導體IT最大任務在於改善產線良率,降低生產成本,替公司創造最大的產能。」陳如經這麼說。
他表示,現在已開始蒐集各項生產製造過程的工程資料,以做為將來大數據分析、機器學習訓練使用。另外也規畫導入無人搬運車與機器手臂,整合MES系統,達到產線生產全自動的目標,減少人力的需求。
CIO小檔案
陳如經
瑞峰半導體資訊管理部處長
學歷:成功大學電機所計算機組碩士
經歷:在半導體IT累積30年資歷,曾是催生世界先進的工研院「次微米計畫」團隊早期成員,並先後任職於世界先進、台積電,負責資料庫、MIS及MES系統的開發建置與維運,並於2016年12月正式擔任瑞峰半導體資訊管理部處長,肩負起從無到有打造IT的重責大任
公司檔案
瑞峰半導體
● 地址:新竹縣湖口鄉新竹工業區光復北路12號
● 網址:www.rayteksemi.com
● 成立時間:2016年
● 主要業務:先進晶圓封裝等半導體製造
● 員工數:約80人
● 資本額:約12億元
● 總經理:戴國瑞
資訊部門檔案
● 資訊部門主管職稱:處長
● 資訊部門主管姓名:陳如經
● 資訊部門名稱:資訊管理部
● 資訊部門人數:5人
● 資訊部門分工:系統維運、製造系統、管理系統
● IT預算:約5,500萬元(2016年系統建置費用)
IT大事記
● 2017年1月:製造執行系統(MES)正式上線、伺服器導入虛擬化
● 2017年3月:開始著手導入ERP系統
● 2017年5月:完成設備自動化計畫(EAP)系統上線
● 2017年8月:配方管理系統(RMS)上線、統計製程控制系統(SPC)系統推出上線
● 2017年10月:ERP系統正式上線
● 2018年6月:晶圓刻號自動比對系統推出上線
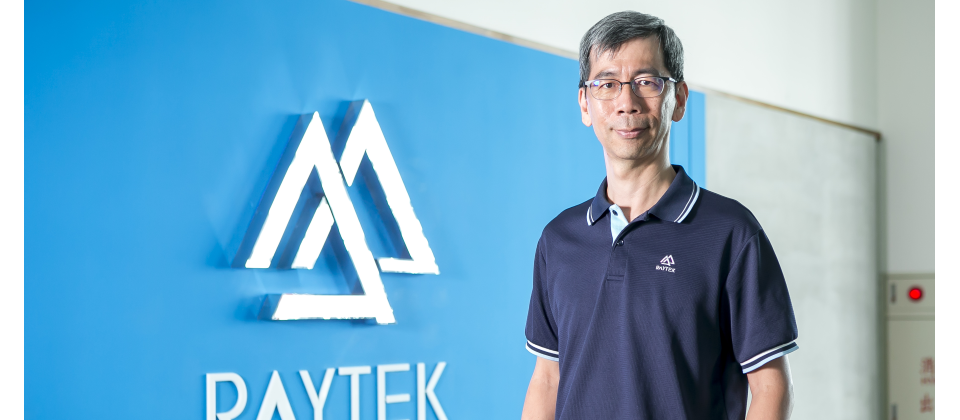